1. Theoretische Prüfung und Analyse
Von den 3ReifenventileVon der Firma bereitgestellte Proben, 2 sind Ventile und 1 ist ein Ventil, das noch nicht verwendet wurde. Bei A und B ist das Ventil, das nicht verwendet wurde, grau markiert. Umfassende Abbildung 1. Die Außenfläche von Ventil A ist flach, die Außenfläche von Ventil B ist die Oberfläche, die Außenfläche von Ventil C ist die Oberfläche und die Außenfläche von Ventil C ist die Oberfläche. Ventile A und B sind mit Korrosionsprodukten bedeckt. Die Ventile A und B sind an den Biegungen gerissen, der äußere Teil der Biegung verläuft entlang des Ventils, die Ventilringöffnung B ist zum Ende hin gerissen und der weiße Pfeil zwischen den gerissenen Flächen auf der Oberfläche von Ventil A ist markiert. Wie oben gezeigt, sind die Risse überall, die Risse sind am größten und die Risse sind überall.
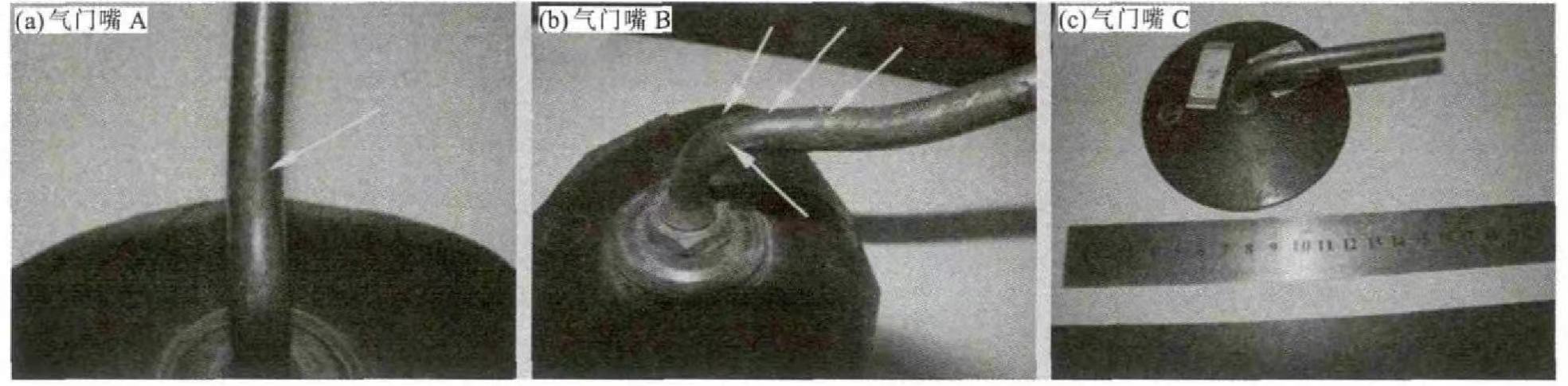
Ein Abschnitt desReifenventilDie Proben A, B und C wurden aus der Biegung geschnitten. Die Oberflächenmorphologie wurde mit einem ZEISS-SUPRA55 Rasterelektronenmikroskop untersucht und die Mikroflächenzusammensetzung mittels EDS analysiert. Abbildung 2 (a) zeigt die Mikrostruktur der Ventiloberfläche B. Man erkennt, dass sich auf der Oberfläche viele weiße und helle Partikel befinden (in der Abbildung durch die weißen Pfeile gekennzeichnet), und die EDS-Analyse der weißen Partikel weist einen hohen S-Gehalt auf. Die Ergebnisse der Energiespektrumanalyse der weißen Partikel sind in Abbildung 2 (b) dargestellt.
Abbildungen 2 (c) und (e) zeigen die Oberflächenmikrostrukturen von Ventil B. Abbildung 2 (c) lässt erkennen, dass die Oberfläche fast vollständig mit Korrosionsprodukten bedeckt ist. Die korrosiven Elemente der Korrosionsprodukte umfassen laut Energiespektrumanalyse hauptsächlich S, Cl und O. Der S-Gehalt an einzelnen Positionen ist höher. Die Ergebnisse der Energiespektrumanalyse sind in Abbildung 2 (d) dargestellt. Abbildung 2 (e) zeigt, dass sich auf der Oberfläche von Ventil A entlang des Ventilrings Mikrorisse befinden. Abbildungen 2 (f) und (g) zeigen die Oberflächenmikromorphologien von Ventil C. Die Oberfläche ist ebenfalls vollständig mit Korrosionsprodukten bedeckt. Die korrosiven Elemente umfassen ebenfalls S, Cl und O, ähnlich wie in Abbildung 2 (e). Die Ursache der Rissbildung kann Spannungsrisskorrosion (SCC) sein, wie aus der Korrosionsproduktanalyse auf der Ventiloberfläche hervorgeht. Abb. 2(h) zeigt die Oberflächenmikrostruktur von Ventil C. Die Oberfläche ist relativ sauber, und die mittels EDS analysierte chemische Zusammensetzung ähnelt der der Kupferlegierung. Dies deutet darauf hin, dass das Ventil nicht korrodiert ist. Ein Vergleich der mikroskopischen Morphologie und der chemischen Zusammensetzung der drei Ventiloberflächen zeigt, dass sich in der Umgebung korrosive Medien wie S, O und Cl befinden.
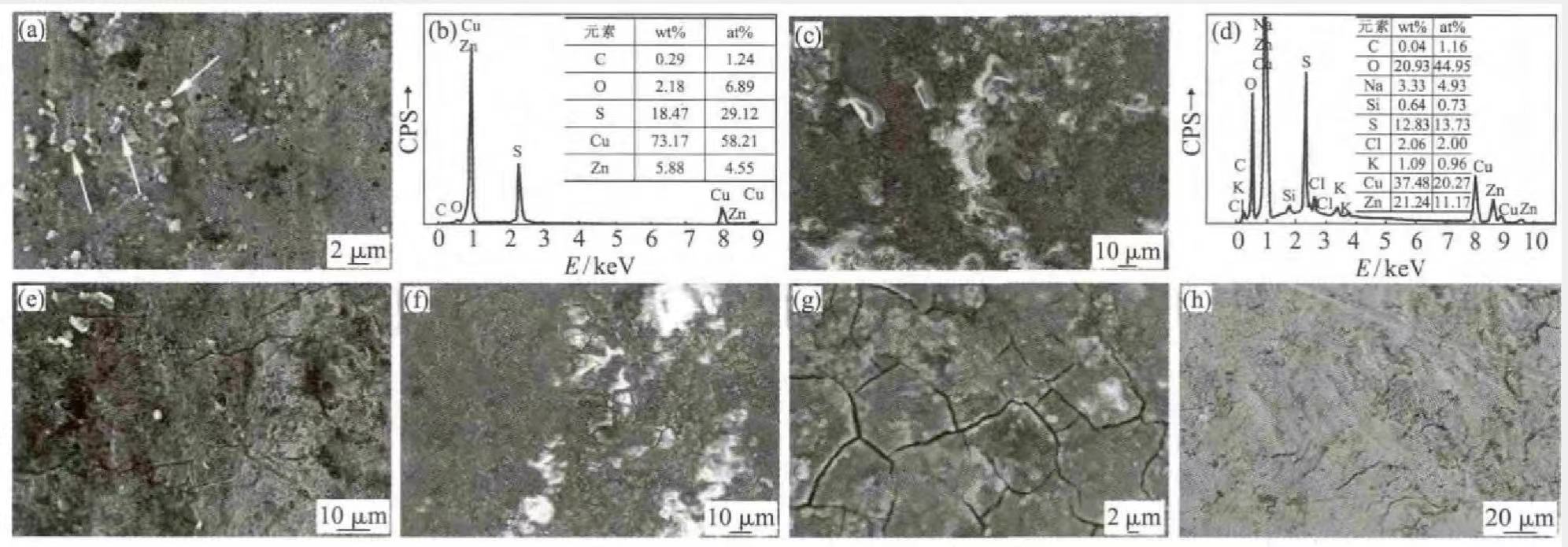
Der Riss von Ventil B wurde im Biegeversuch geöffnet. Dabei zeigte sich, dass der Riss nicht den gesamten Querschnitt des Ventils durchdrang, sondern auf der Seite der Rückbiegung und auf der der Rückbiegung gegenüberliegenden Seite des Ventils riss. Die visuelle Untersuchung des Bruchs zeigt eine dunkle Färbung, die auf Korrosion hindeutet. Einige Bereiche des Bruchs sind dunkel gefärbt, was auf eine stärkere Korrosion hindeutet. Der Bruch von Ventil B wurde unter einem Rasterelektronenmikroskop untersucht (siehe Abbildung 3). Abbildung 3 (a) zeigt das makroskopische Erscheinungsbild des Bruchs von Ventil B. Es ist zu erkennen, dass der äußere Bruch in der Nähe des Ventils mit Korrosionsprodukten bedeckt ist, was wiederum auf korrosive Medien in der Umgebung hinweist. Laut Energiespektrumanalyse bestehen die chemischen Bestandteile des Korrosionsprodukts hauptsächlich aus S, Cl und O, wobei die S- und O-Gehalte relativ hoch sind (siehe Abbildung 3 (b)). Bei Betrachtung der Bruchoberfläche zeigt sich ein kristallförmiges Risswachstumsmuster. Eine große Anzahl von Sekundärrissen ist auch bei stärkerer Vergrößerung des Bruchs erkennbar, wie in Abbildung 3(c) dargestellt. Die Sekundärrisse sind in der Abbildung mit weißen Pfeilen markiert. Korrosionsprodukte und Risswachstumsmuster auf der Bruchoberfläche weisen ebenfalls die Merkmale der Spannungsrisskorrosion auf.
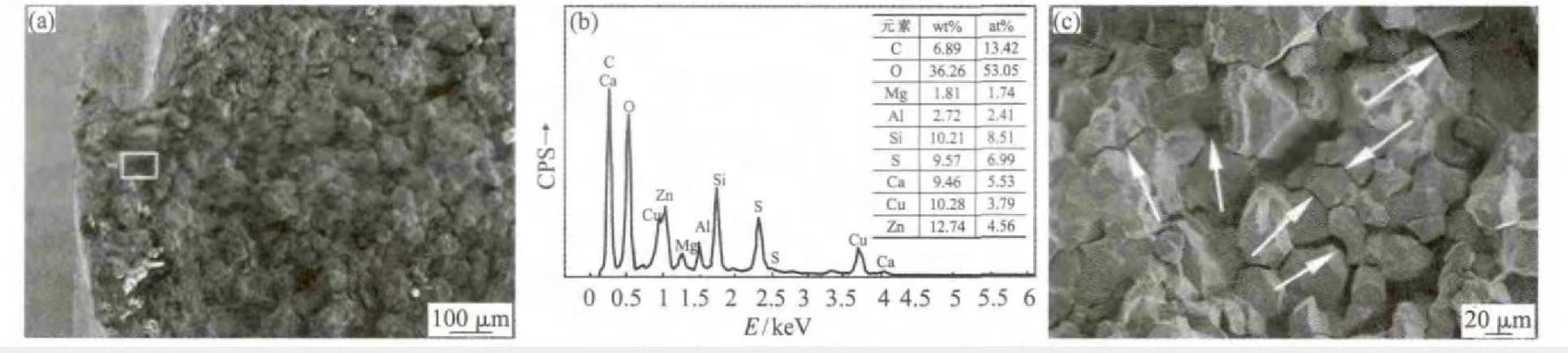
Der Bruch von Ventil A wurde nicht geöffnet. Entfernen Sie einen Abschnitt des Ventils (einschließlich der Rissstelle), schleifen und polieren Sie den axialen Abschnitt des Ventils und verwenden Sie eine Lösung aus FeCl3 (5 g) + HCl (50 ml) + C2H5OH (100 ml). Es wurde geätzt und die metallografische Struktur und die Morphologie des Risswachstums wurden mit einem optischen Mikroskop Zeiss Axio Observer A1m beobachtet. Abbildung 4 (a) zeigt die metallografische Struktur des Ventils, die eine α+β-Doppelphasenstruktur aufweist, und β ist relativ fein und körnig und auf der α-Phasenmatrix verteilt. Die Rissausbreitungsmuster an den Umfangsrissen sind in Abbildung 4 (a) und (b) dargestellt. Da die Rissoberflächen mit Korrosionsprodukten gefüllt sind, ist der Spalt zwischen den beiden Rissoberflächen groß und es ist schwierig, die Rissausbreitungsmuster zu unterscheiden. Bifurkationsphänomen. Auf diesem Hauptriss wurden auch viele Sekundärrisse (in der Abbildung mit weißen Pfeilen markiert) beobachtet, siehe Abb. 4(c) und diese Sekundärrisse breiteten sich entlang der Maserung aus. Die geätzte Ventilprobe wurde mittels SEM untersucht und dabei wurden zahlreiche Mikrorisse an anderen Stellen parallel zum Hauptriss festgestellt. Diese Mikrorisse gingen von der Oberfläche aus und breiteten sich ins Innere des Ventils aus. Die Risse waren verzweigt und verliefen entlang der Maserung, siehe Abb. 4(c),(d). Umgebung und Spannungszustand dieser Mikrorisse sind nahezu identisch mit denen des Hauptrisses, sodass man davon ausgehen kann, dass die Ausbreitungsform des Hauptrisses ebenfalls intergranular ist, was auch durch die Bruchbeobachtung von Ventil B bestätigt wird. Das Verzweigungsphänomen des Risses weist erneut die Merkmale der Spannungsrisskorrosion des Ventils auf.
2. Analyse und Diskussion
Zusammenfassend lässt sich sagen, dass der Schaden am Ventil durch Spannungsrisskorrosion durch SO2 verursacht wurde. Spannungsrisskorrosion muss im Allgemeinen drei Bedingungen erfüllen: (1) Materialien, die empfindlich auf Spannungsrisskorrosion reagieren; (2) korrosives Medium, das empfindlich auf Kupferlegierungen reagiert; (3) bestimmte Spannungsbedingungen.
Es wird allgemein angenommen, dass reine Metalle nicht unter Spannungsrisskorrosion leiden und alle Legierungen in unterschiedlichem Ausmaß dazu neigen. Bei Messingwerkstoffen wird allgemein angenommen, dass die Zweiphasenstruktur anfälliger für Spannungsrisskorrosion ist als die Einphasenstruktur. In der Literatur wird berichtet, dass Messingwerkstoffe ab einem Zn-Gehalt von 20 % anfälliger für Spannungsrisskorrosion sind, und zwar mit steigendem Zn-Gehalt. Die metallografische Struktur der Gasdüse ist in diesem Fall eine α+β-Zweiphasenlegierung. Der Zn-Gehalt beträgt etwa 35 %, also weit über 20 %. Daher ist die Legierung anfälliger für Spannungsrisskorrosion und erfüllt die Materialbedingungen für Spannungsrisskorrosion.
Bei Messingwerkstoffen tritt unter geeigneten Spannungsbedingungen und in korrosiver Umgebung Spannungsrisskorrosion auf, wenn nach der Kaltverformung kein Spannungsarmglühen durchgeführt wird. Die Spannung, die Spannungsrisskorrosion verursacht, ist in der Regel lokale Zugspannung, die sowohl als Eigenspannung als auch als angelegte Spannung auftreten kann. Nach dem Aufpumpen eines LKW-Reifens entsteht aufgrund des hohen Reifendrucks eine Zugspannung entlang der Düsenachse, die zu umlaufenden Rissen in der Düse führt. Die durch den Reifeninnendruck verursachte Zugspannung lässt sich einfach nach σ = p R/2t berechnen (wobei p der Reifeninnendruck, R der Ventilinnendurchmesser und t die Ventilwandstärke ist). Im Allgemeinen ist die durch den Reifeninnendruck erzeugte Zugspannung jedoch nicht zu groß, sodass der Einfluss der Eigenspannung berücksichtigt werden sollte. Die Risse der Gasdüsen befinden sich alle an der Rückbiegung. Es ist offensichtlich, dass die Eigenverformung dort groß ist und eine Eigenzugspannung vorhanden ist. Tatsächlich wird Spannungsrisskorrosion bei vielen praktischen Kupferlegierungskomponenten selten durch konstruktionsbedingte Spannungen verursacht, sondern meist durch unbemerkte und ignorierte Eigenspannungen. In diesem Fall stimmt an der Ventilrückbiegung die Richtung der durch den Reifeninnendruck erzeugten Zugspannung mit der Richtung der Eigenspannung überein, und die Überlagerung dieser beiden Spannungen liefert die Spannungsbedingung für die Spannungsrisskorrosion.
3. Schlussfolgerung und Vorschläge
Abschluss:
Das Knacken derReifenventilwird hauptsächlich durch Spannungsrisskorrosion verursacht, die durch SO2 verursacht wird.
Anregung
(1) Die Quelle des korrosiven Mediums in der Umgebung desReifenventilund versuchen Sie, den direkten Kontakt mit dem umgebenden korrosiven Medium zu vermeiden. Beispielsweise kann eine Schicht Korrosionsschutzbeschichtung auf die Oberfläche des Ventils aufgetragen werden.
(2) Die bei der Kaltverformung entstehenden Zugeigenspannungen können durch geeignete Verfahren, wie beispielsweise Spannungsarmglühen nach dem Biegen, beseitigt werden.
Veröffentlichungszeit: 23.09.2022